Custom Insert Molding Process Services
PMC offers custom insert molding, a specialized plastic injection molding process where plastic is injected into a mold cavity, surrounding an insert piece (or multiple pieces) placed in the cavity just before molding. This process results in a single, durable piece where the insert is securely encapsulated by the plastic material.
Advantages of Insert Molding
The insert molding process expands the possibilities of plastic manufacturing by allowing various materials, such as metal or other plastics, to be integrated into a single molded piece. This method can lower overall production costs by reducing the use of expensive metals and creating a lighter, more efficient part. Initially developed to add threaded inserts in plastic parts and encapsulate wire connections in electrical cords, insert molding now offers a broad range of uses across industries.
Capabilities Beyond Standard Molding
At PMC, we extend insert molding capabilities to achieve results that other molders may find challenging. We can manufacture multi-cavity molds, depending on part size, to increase production efficiency. Additionally, we provide secondary post-molding operations as needed to complete the assembly, offering a seamless, high-quality finish to your product.
Why Choose PMC for Insert Molding?
Expertise in Complex Insert Molding
Our team has the experience to handle challenging insert molding projects, ensuring high precision and quality.
Advanced Production Capabilities
We offer multi-cavity molds for larger-scale production and provide post-molding operations to streamline assembly.
Cost-Effective Solutions
By encapsulating metal or other materials within plastic, we help reduce material costs and produce lighter parts without sacrificing strength.
Commitment to Quality
Our insert molding process ensures that each piece meets rigorous quality standards, providing a durable and reliable final product.
Custom Insert Molding Gallery
Check out examples of our custom insert plastic injection molding using our specialized filtration application.
Custom Insert Molding of Micron-Rated Screens
Filtration is a specialized application of insert molding. The engineers at PMC have years of training and experience developing innovative filtration & contamination control solutions for a broad range of commercial applications. These include custom filters for drinking water, paint, small and large appliances, heavy equipment and recreational vehicles.
If you’ve ever experienced a catastrophic product failure caused by contamination, you’re intimately aware that there’s more to designing custom filters than simply fitting filtration within an allotted space.
Our engineers think outside the box when it comes to filter and screen design, generating ideas that are both effective in controlling contaminants and cost-effective to produce.
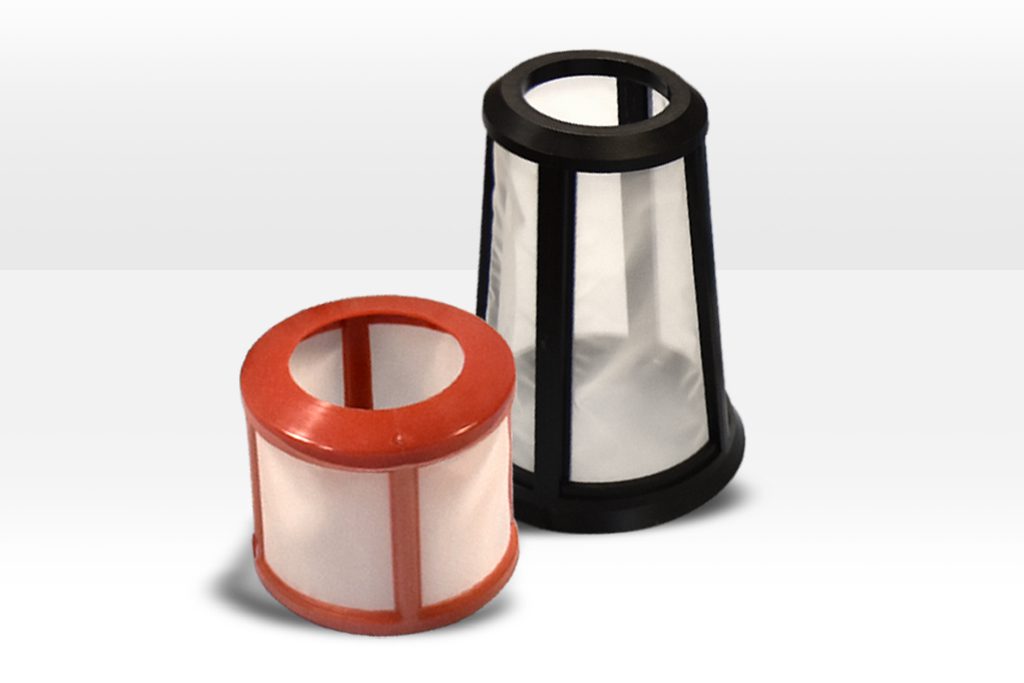
Request quote
Plastic Molded Concepts creates and ships parts that our customers can use with confidence, security, and safety.